Lean processes in body and paint stores
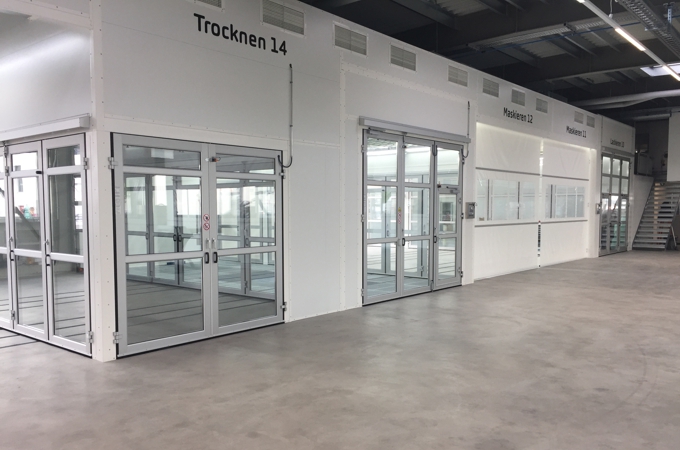
Lean processes in paint and body stores increase the profitability of the company. A key factor in this is perfect vehicle routing. In addition, modern plant and machinery are crucial to the efficiency of operations. The German paint shop manufacturer SEHON shows which large and small adjusting screws can make the difference between success and failure.
Vehicle routing decides
In classic routing, a vehicle passes through the process chain of preparation workstation – paint booth – dryer.
The first starting point for improving this process is to connect the paint booth and dryer with a folding sliding door and simply transport the vehicle from the paint booth to the dryer without using the engine or moving it back and forth by manually pushing it across.
This is not only particularly environmentally friendly, but also saves valuable time.
Paint stores are now networking the main processes with a continuous rail system that allows the vehicles to be moved easily and simply from process to process.
Activate masking
In many companies, the paint booth is used as a masking workstation.
This takes the booth away from its actual task.
The booth is unnecessarily blocked for the painting process.
Another drawback of this approach is that the paint booth is unnecessarily enriched with dirt particles and foreign substances as a result of masking work.
This ultimately affects the quality of the paint finish.
The costs for finishing and reworking increase.
It is therefore becoming increasingly common to plan a separate masking area in the painting and drying process, so that the masking – painting – drying process is created.
The result of this process chain is cleaner paint booths, more painting capacity, better quality and less finishing work.
SEHON’s cleanroom concept is a good example of how process changes can bring both time and quality benefits.
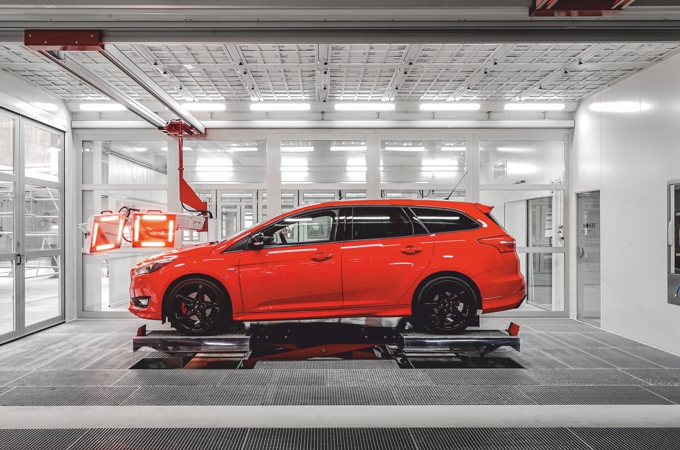
Multifunctional spray booth, instead of a standard spray booth.
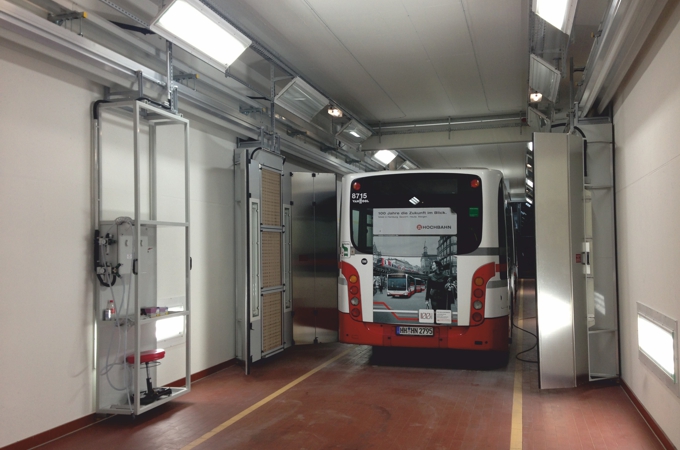
Spot repair system for the repair of road vehicles.
Using multi-paint booths
When building new paint and bodywork centers, perfect process planning can ensure high throughput speeds and maximum efficiency from the outset.
One option is to plan the workflow as in industrial-style production lines.
The vehicles run through a process chain similar to an assembly line.
Another interesting workflow plan extends the classic paint booth + dryer to include the separate masking station described above and two multifunctional booths.
In this specific case, the customer deliberately decided against a second recirculating air paint booth and a second recirculating air dryer.
Instead, two SE-PROFESSIONAL MULTISTAR multi-coating booths with infrared dryers were installed in the process chain.
This decision is based on two solid reasons.
The first reason is that major accident repairs are continuously decreasing thanks to modern vehicle safety technologies.
Nevertheless, accidents with minor damage are increasing.
For bodyshops, this continuing trend means that they need to focus on minor damage repairs, for which there are better economic alternatives to the classic paint booth and dryer.
SEHON multifunctional paint booths are fully-fledged paint booths with infrared drying, which are ideal for small damage repairs including spot repairs.
The big advantage is that all process steps from filler to finish can be carried out in this booth at a single workstation without having to move the vehicle around.
The second important reason for integrating a multi-paint booth is internal damage control.
If a multi-paint booth is integrated into the process chain, accident vehicles can be directed to the correct processing technology from the outset.
Depending on the type and extent of damage, either in the classic paint booth with subsequent dryer or directly in the multifunctional booth for fast and economical small damage repairs.
Process-oriented workstations
Existing plants in particular can hardly change the vehicle routing due to fixed spatial conditions.
However, multi-painting booths and separate masking workstations can be retrofitted.
Existing or redundant classic preparation stations are usually used for this purpose.
Spot repair
SEHON Multi-Speed-Master professional spot repair workstations are an alternative to a multi-paint booth for small damage repairs.
These spot repair workstations are suitable for retrofitting in the space of a standard preparation area.
The Multi-Speed-Master is also an all-in-one workstation at which all preparation – painting – drying – finishing work can be carried out quickly and efficiently.
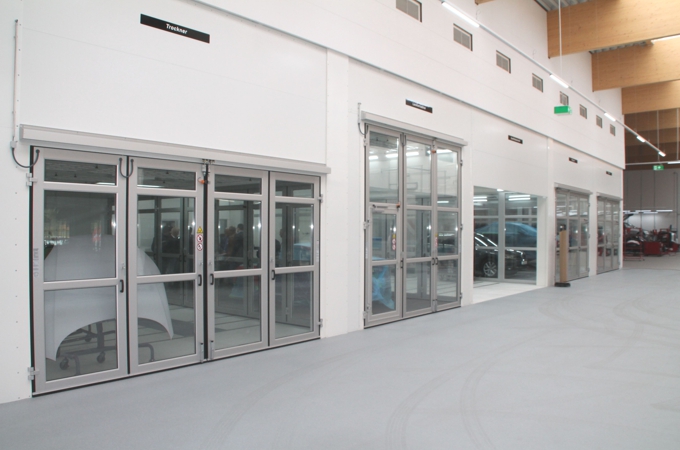
Process-oriented painting systems implemented in series according to the workflow principle.
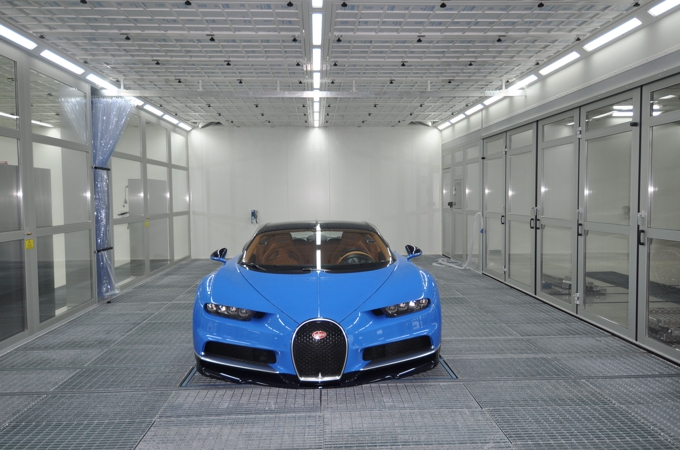
Combination spray booth with continuous grating for perfect extraction.
Car body workstations for steel, aluminum and carbon
More and more vehicles are made from a mix of different materials.
Legislation stipulates that different materials must be processed at different material-related workstations for safety reasons.
As if every body store had to have a separate body work station for each material.
In practice, things usually look different.
Anyone who repairs various materials such as aluminum and carbon on the existing body work station for steel is literally playing with fire.
This can lead to serious explosions and dangerous injuries to employees.
Company owners very often fail to realize that they alone are responsible for operational safety.
As the CAMELEON all-in-one bodywork workstation means that only one workstation is required instead of a large number of different bodywork workstations, CAMELEON from SEHON is a process-oriented workstation that saves time and money.
And not to be underestimated: absolute safety when repairing mixed-material vehicles.
Central supply terminals
With the SE-MEGA-SUPPLIER central supply terminal, SEHON has created a very popular product for greater efficiency and safety at preparation, body and finishing workstations.
The supply terminal contains all the important connections that are needed at the respective workstation, putting an end to the mess of cables for the various connections.
The supply terminal integrates various connections for power supply, compressed air, sanding machines (electric/pneumatic), sanding dust extraction, spray guns, lifting platforms and diagnostics in a central, compact and clean way.
Special requests such as an integrated sound system are also possible.
This enables highly efficient, ergonomic and process-oriented working at a wide variety of workstations.
Contact: sehon-lackieranlagen.de | info@sehon.de
Author: Michael Teschke, June 2, 2019 | Photos: Sehon